Accidents continue to happen — more and more frequently — at U.S. Steel.
Three workers have died at U.S. Steel mills since September, according to United Steelworkers union officials: a crane operator at the Gary Works (Ind.) in September; a management employee at Gary who died of carbon monoxide poisoning in December; and a union worker who was crushed by a slow-moving train this month at the Granite City Works in Illinois.
Union workers at U.S. Steel’s Clairton Works in Pennsylvania held a protest rally over safety in August after a 44-year-old union worker lost his legs in a train accident.
Favorable business conditions have spurred speculation that the pressure on workers to produce may be making mills less safe. A 2003 labor agreement with the USW that radically altered the makeup of the work force and their job responsibilities is also being blamed.
“I’m not sure you can put it all on [the labor agreement]. I think it plays a part in it,” said Michael Mitchell, president of USW Local 1014 at U.S. Steel’s Gary Works.
Mitchell believes pressure to produce, increased overtime because of work force reductions and lack of training are other possible causes. “Until all those things are looked at … [accidents] are going to continue to happen,” he said. “We have a terrible safety record as far as accidents and fatalities.”
The new agreement, patterned after other contracts used to resurrect bankrupt steelmakers, rewrote the book on how dozens of mills jobs are performed and who must perform them. Simultaneously, many of the industry’s most experienced workers were given incentives to retire in order to reduce labor costs.
Consequently, workers who remained are being asked to do new jobs, and seasoned workers are not around to help them.
“We need more training,” said Steve Tunello, president of USW Local 1013 at U.S. Steel’s Fairfield Works in Alabama. “I imagine we’re a lot like Clairton. We need more people.”
Mike Wright, the union’s top health and safety officer, said U.S. Steel is more concerned about making safety a disciplinary problem than getting at the root cause of the accidents. “U.S. Steel is stuck on this idea that their problems are based on employee misconduct,” Wright said. “The way to get after safety problems is to comprehensively analyze the safety of every job in the plant.”
Blame the worker?
Like many employers, U.S. Steel is buying into the classic “blame the worker” theory and relying on “behavioral safety” as the solution. Behavioral safety theories say that worker carelessness or misconduct is the cause of most accidents, and disciplining workers is the answer. But behavioral theories don’t hold up to a closer look at the cause of most workplace accidents.
Ultimately, of course, most accidents are caused by someone doing something “wrong.” That’s generally known as the “direct cause.” If that’s where your analysis of the accident stops, the obvious answer is to find out who made the mistake and fire his ass. Problem solved. Right?
Wrong. If you really want to prevent future similar accidents, you need to go further and look for the root causes. The simplest way to do that is to keep asking “why?” Someone used the wrong equipment, or pressed the wrong button. Why? Were they told to do it by a supervisor who had a quota to fill? Did they feel rushed by the constant drive for more productivity? Were they not well trained for the job? Were they tired from too much overtime? Were the controls on the machine unnecessarily complicated or not logically located? Was there an unexpected confluence of unexpected problems caused somewhere else in the system that no one knew how to handle?
If an accident was caused by someone using the wrong equipment because they were being pressured to rush and the correct equipment would have taken too long to locate and set up, then firing that worker isn’t going to solve the problem. The next guy will be in exactly the same situation. Which is why Wright is insisting that every job be thoroughly analyzed.
U.S. Steel’s answer is to schedule mandatory safety meetings led by top executives for hourly and management workers that will feature a videotaped message from U.S. Steel President John P. Surma.
Reprinted with permission from Confined Space (spewingforth.blogspot.com)
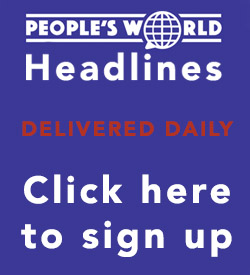
Comments